负载传感系统基础
例如,当电流施加到SP1的其中一个线圈上时,油流过EC1、SP1,最后从A1或B1的工作油口流出。当A1处的执行器移动时,它对液压系统施加一个负载。这个负载压力通过SP1的负载传感油口传递出去,并进一步传递到功能补偿器上。最终,负载压力通过负载传感网络,跨过负载传感单向阀(CV1至CV3),传到主负载传感管路。
选择多个功能
当多个功能同时操作时,只允许最高的负载传感信号通过这些单向阀之一传递到主线上。当操作员要求执行器提供更大速度(压力不一定随着功能流量增加而增加)和/或如果负载压力因阻力而增加时,负载传感压力会增加。EPFR1会响应负载压力的变化而打开或关闭。
这改变了泵到油箱通道的节流,从而使液压控制回路中可用流量减少或增多。最终,系统能发展的最大压力由溢流阀RV1的设定值调节。
三个功能同时运行
一个典型的操作场景可能是所有三个功能同时运行。假设A2和B2之间的负载阻力最大。负载压力通过CV2传递。这个压力作用在EPFR1上,它响应此压力而关闭。系统压力增加,增加量为移动A2或B2处负载所需的压力加上EPFR1的弹簧值。随着负载压力需求的增加,最终EPFR1将完全关闭,所有流量都将可用于移动执行器,直到压力等于RV1的设定值。然后流量将开始通过RV1溢出。这个系统压力被施加到所有三个工作功能的进口。各个功能补偿阀(EC1, EC2和EC3)将限制这个压力到每个功能,以确保每个SP阀两端有一致的压差。因此,每个执行器的速度是基于给定工作功能下阀芯的开度来控制的,而不是进口压力的函数。
插装阀是构建模块
除了设计合理的负载传感系统带来的明显效率优势外,HydraForce回路还将充分利用为每个单独应用定制的优势。插装阀是液压世界的构建模块,可以被布置并安装到一个定制的集成块中,从而无需外部连接单个阀门。此外,可以为每个执行器选择相对于流量需求的正确尺寸的插装阀。因此,阀门组件的成本和尺寸都减小了,同时性能也得到了改善。
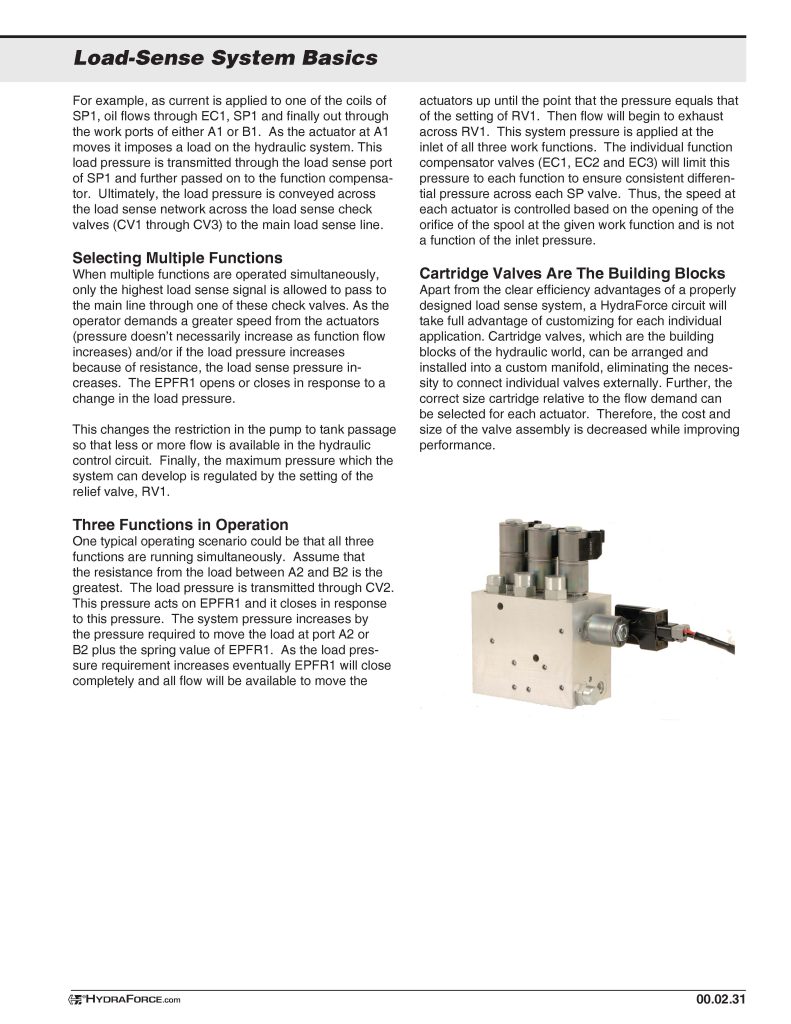